Everything You Need to Know about Large 3D Printing
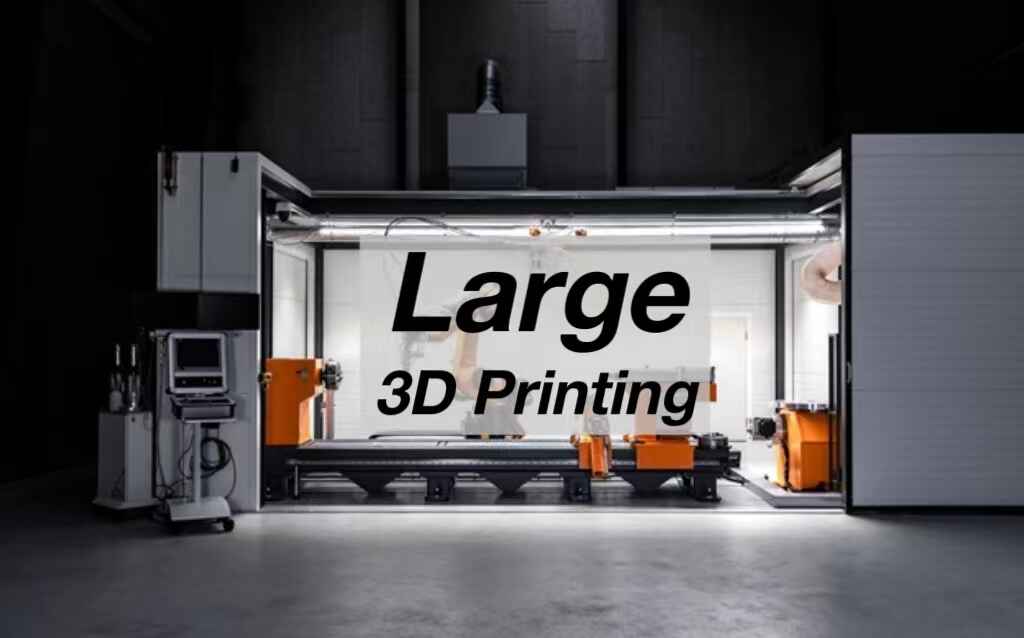
Discover how large 3D printing works, what materials and technologies are used, and which providers offer the best solutions for industrial-scale production.
Introduction
What if you could print a car dashboard in one piece — full-size, ready to test — with no tooling, no molds, and no weeks-long delays? That’s the promise of large-format 3D printing.
By scaling additive manufacturing to new dimensions, large 3D printing gives engineers, designers, and manufacturers the power to build bigger, faster, and smarter.
In this guide, you'll learn how large-format 3D printing works, what materials and technologies power it, how companies are using it today, and what to look for when choosing the provider for your next big build.
[View Unionfab’s Large 3D Printing capabilities here →]
What is Large 3D Printing?
Large-format 3D printing — also known as large-scale additive manufacturing — is the process of producing oversized parts using industrial-grade 3D printers with build volumes often exceeding 1 cubic meter.
These machines are designed to print components that are simply too big, too complex, or too expensive to manufacture using traditional methods or standard desktop printers.
Unlike conventional fabrication that relies on molds, welds, or multi-part assembly, large-format 3D printing allows you to create single-piece, full-scale parts directly from digital files. Think:
Full-size automotive body panels
Architectural façades and columns
Industrial molds, jigs, and fixtures
Custom furniture, signage, and display structures ⠀
It’s fast, flexible, and increasingly production-ready.
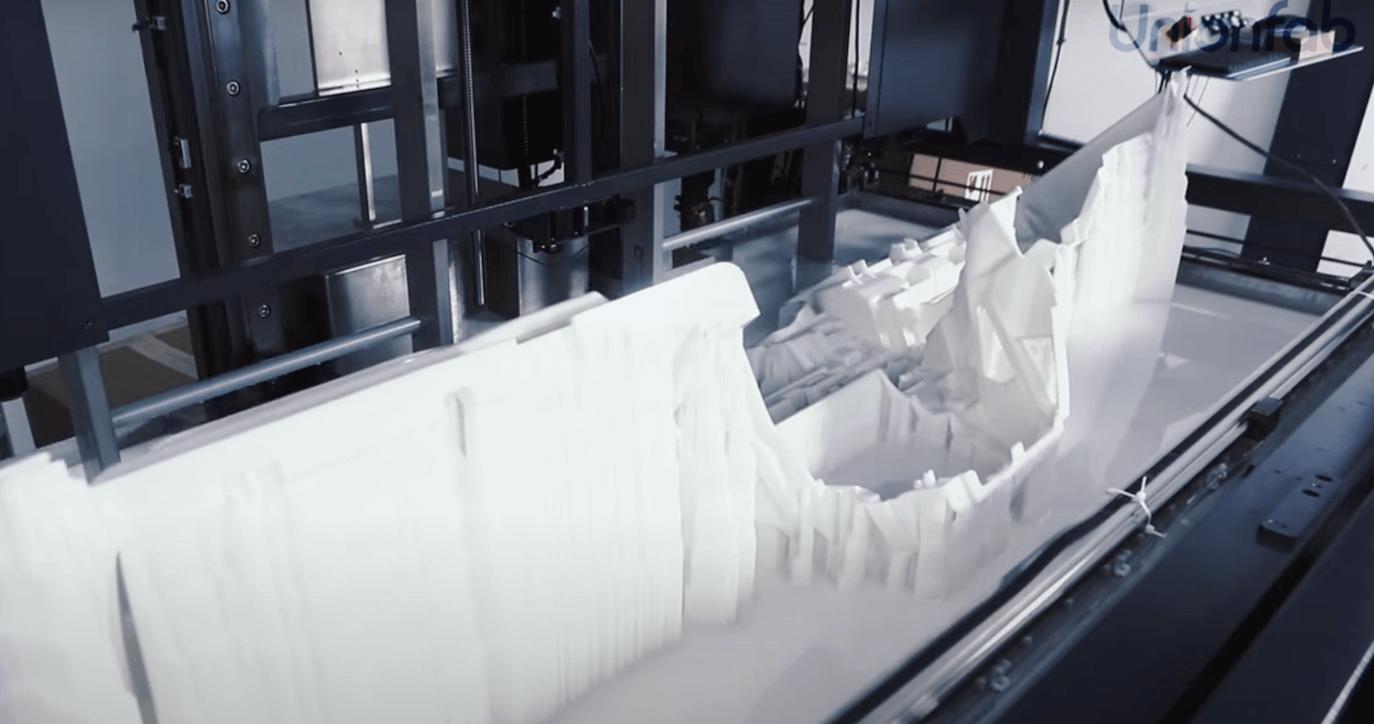
Core Technologies Behind Large-Scale 3D Printing
Technology | Ideal For | Typical Materials | Max Size | Approx. Material Cost | Pros | Cons |
---|---|---|---|---|---|---|
Low-cost prototypes, large fixtures, furniture | PLA, ABS, PETG, Nylon, CF-filled | Multi-meter | $20–$60/kg | Cheap, scalable, easy setup | Coarse surface, layer lines, support needed | |
High-detail prototypes, smooth models, art pieces | Photopolymer resins | Up to ~2100 × 700 × 800 mm | $50–$200/kg | Excellent resolution & finish | Brittle, expensive resin, support removal | |
Functional nylon parts, small batch production | Nylon (PA12, PA11), TPU | ~600–700 mm per side | ~$100/kg | Strong, no support needed, complex geometry | Grainy finish, costly setup | |
WAAM | Large metal parts, tools, molds | Steel, Aluminum, Titanium (wire) | Unlimited | $15–$100/kg | Big metal parts fast, cheap material | Rough surface, post-machining required |
Sand molds, batch metal parts | Sand, Metal powders | Sand: ~1800 mm; Metal: ~300–500 mm | Sand: <$1/kg; Metal: ~$50–$100/kg | Fast for molds, no supports, batch-friendly | Needs sintering/casting, shrinkage, fragile pre-processing |
As the demand for rapid, tool-free production of large components grows across sectors, large-format 3D printing is no longer a niche — it's a competitive advantage.
When to Choose Which Large 3D Printing Technology
Situation/Requirement | Recommended 3D Printing Process |
---|---|
Budget is very limited, relatively simple and very large part needed; tolerances not critical | FDM/FFF – Cheapest for big, basic shapes. Full-scale appliance mock-ups, furniture panels, basic jigs. |
High-detail, smooth surface, or aesthetic model (appearance prototype) | SLA – Best surface finish for visual models. Design prototypes, art pieces, cosmetic covers, jewelry molds. |
Complex geometry, functional plastic part (durable, no supports, possibly multiple parts at once) | SLS (or MJF) – Excels at complex, strong prototypes and small batch production. Drone components, snap-fit enclosures, eyewear, low-volume end-use parts |
Extremely large metal part or tooling (one-off or low quantity) | WAAM (DED) – No size limit, avoids costly casting/forging tooling. Aerospace fixtures, automotive dies, structural machine parts |
Need a large metal part but can use casting | Binder Jetting (Sand) – (Print the sand mold, then cast the metal). Example: an engine block prototype or a pump housing without making patterns. |
End-use part needs isotropic strength and smooth finish out of printer | (Consider CNC or other tech) – No additive method gives fully isotropic properties without post-process; however, SLS comes close for plastics, and post-processing like annealing can improve FDM parts. Smooth finish can be achieved via post-processing on any. |
Unsure which one to choose?
Talk to Unionfab Experts
Key Benefits of Large 3D Printing
Large-format 3D printing offers significant advantages over traditional manufacturing and standard-size additive processes, especially when scale, speed, and customization are priorities.
Why Choose Large-Scale 3D Printing?
Large 3D printing for Dior Installment
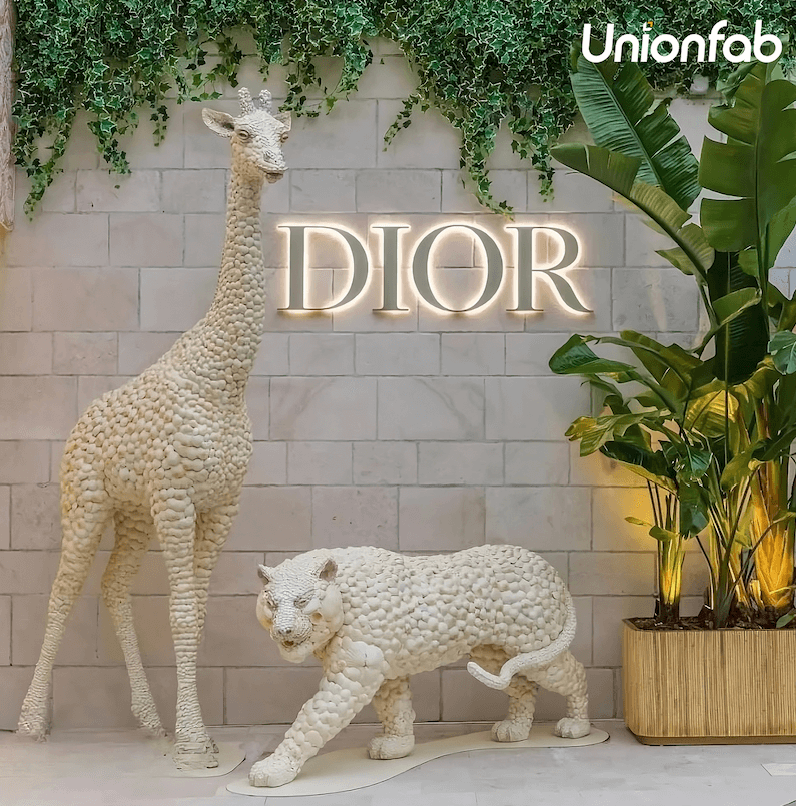
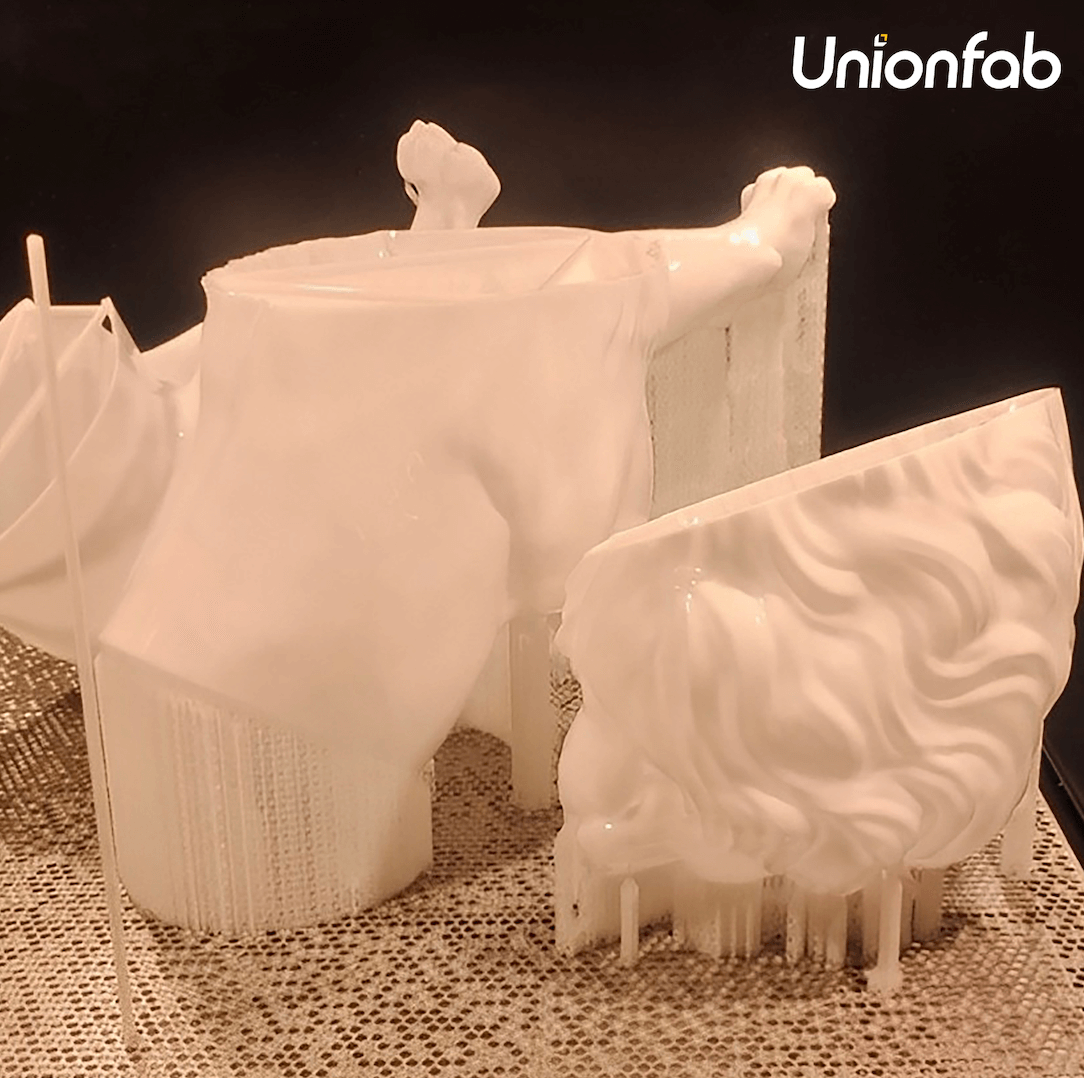
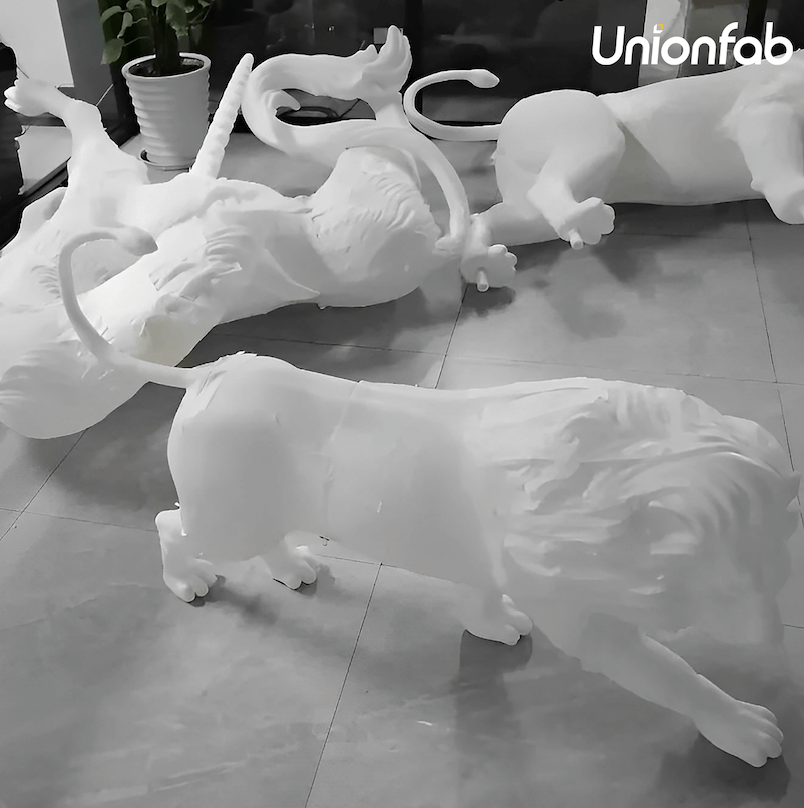
Single-piece, full-scale parts: Eliminate the need for assembly or bonding by printing large components in one go.
Faster turnaround: Drastically reduce lead times for prototypes, molds, and functional parts — often in days instead of weeks.
Cost-effective for low volumes: Avoid high tooling or mold costs, making it ideal for small-batch or one-off productions.
Design freedom: Create complex geometries, hollow structures, or lightweight lattice infills with ease.
Adaptability: Suitable for multiple industries — from automotive to architecture — and a wide range of materials.
Material Options for Large 3D Printing
Material selection is a critical factor in large-format 3D printing. Depending on the application — whether it’s for prototyping, functional parts, or end-use molds — different materials offer unique benefits and trade-offs in strength, weight, surface quality, and cost.
Thermoplastics (FDM/FFF)
Material | Common Uses | Key Benefits | Limitations |
---|---|---|---|
PLA | Large display models, visual prototypes | Low cost, easy to print, eco-friendly | Brittle, low heat resistance |
PETG | Functional parts, jigs, enclosures | Tough, chemical-resistant, low warp | Less rigid than ABS |
ABS | Automotive parts, prototypes | Durable, impact-resistant | Requires controlled environment |
Nylon (PA) | Wear-resistant parts, hinges, tooling | Strong, flexible, low friction | Moisture-sensitive, needs drying |
Carbon-Fiber Reinforced | High-strength brackets, fixtures | Lightweight, high stiffness | Higher material cost, nozzle wear |
Photopolymers (SLA/LFS)
Used for large resin-based models, especially where surface quality and detail are important.
Material Type | Applications | Benefits | Limitations |
---|---|---|---|
Standard Resin | Concept models, art pieces | Smooth surface, fine detail | Brittle, not functional under load |
Tough Resin | Engineering prototypes, functional tests | Impact resistance, higher strength | More expensive, UV-sensitive |
Metals (WAAM, DED)
Wire Arc Additive Manufacturing (WAAM) and Directed Energy Deposition (DED) allow for large-scale metal printing.
Metal Type | Applications | Benefits | Limitations |
---|---|---|---|
Stainless Steel | Tooling, structural parts | Corrosion-resistant, strong | Requires post-machining |
Titanium | Aerospace parts, medical structures | Lightweight, biocompatible | Very expensive, slow to print |
Aluminum | Lightweight components, fixtures | Good strength-to-weight ratio | Lower strength than steel |
Leading Large 3D Printing Providers & Technologies
Here’s a quick look at some of the top players offering industrial-scale 3D printing, and the kind of size, technology, and capabilities they bring to the table:
Provider | Key Technologies | Max Build Volume (mm) | Strengths |
---|---|---|---|
Unionfab | SLA, SLS, FDM, Metal Printing | 2100 × 900 × 700 (SLA) | World's largest SLA fleet, end-to-end service |
FacFox | SLA, SLS, FDM, SLM | 1700 × 800 × 500 (SLA) | Multi-material printing, fast delivery |
Titan Robotics | Pellet-fed FDM | 1270 × 1270 × 1829 | High-throughput for tooling, large parts |
Massivit 3D | GDP (Gel Dispensing Printing) | 1200 × 1500 × 1800 | Giant props, signs, molds |
Voxeljet | Binder Jetting (Sand Molds) | 4000 × 2000 × 1000 | Massive molds for casting |
BigRep | FDM | 1005 × 1005 × 1005 | Durable, architectural-grade parts |
3D Platform | FDM (FFF) | 1000 × 1000 × 700 | Affordable, open-material systems |
Builder 3D | FDM | 1100 × 1100 × 820 | Complex geometries, design flexibility |
Choosing the Right Large-Format Printing Provider
When selecting a partner for large 3D printing, look for:
Criteria | What Unionfab Offers |
---|---|
Print Volume & Technology | Multiple machines up to 1.8m+, hybrid options |
Material Selection | Engineering-grade resin, plastics & composites |
Engineering Support | Dedicated DfAM consultants |
Post-Processing | Full suite in-house (paint, polish, assembly) |
Turnaround Time | Fast lead time, often within 3–10 days |
Global Service | International shipping and project management |
Why Unionfab is Built for Big Ideas
Large 3D printing for car side panel
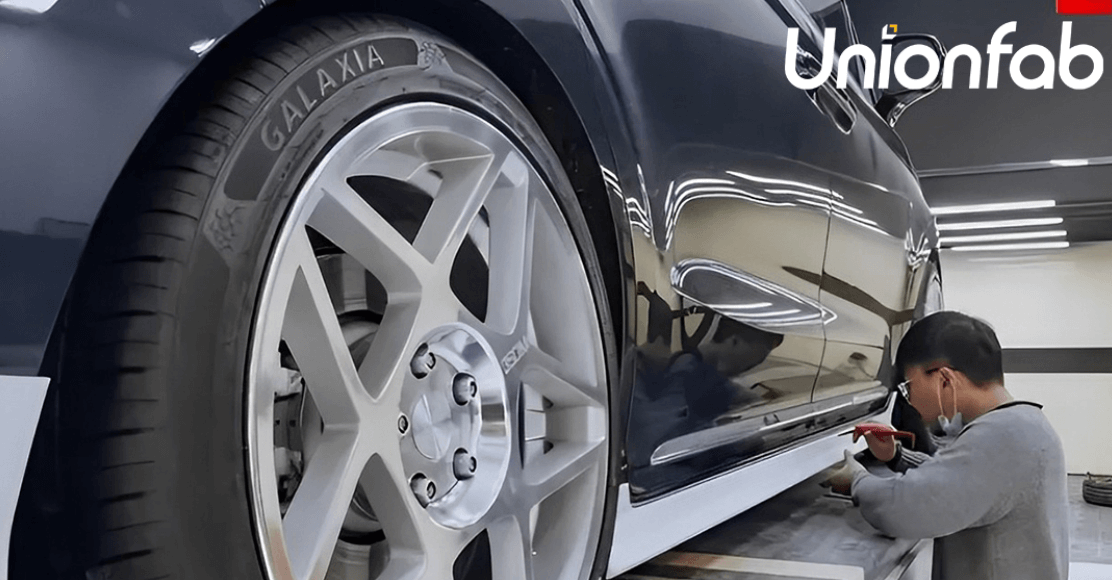
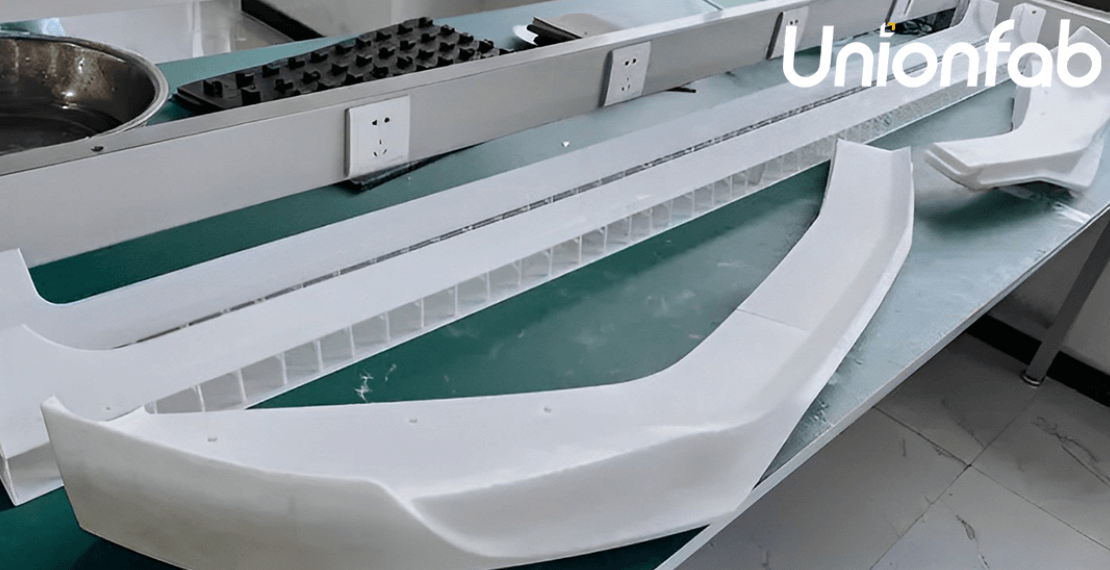
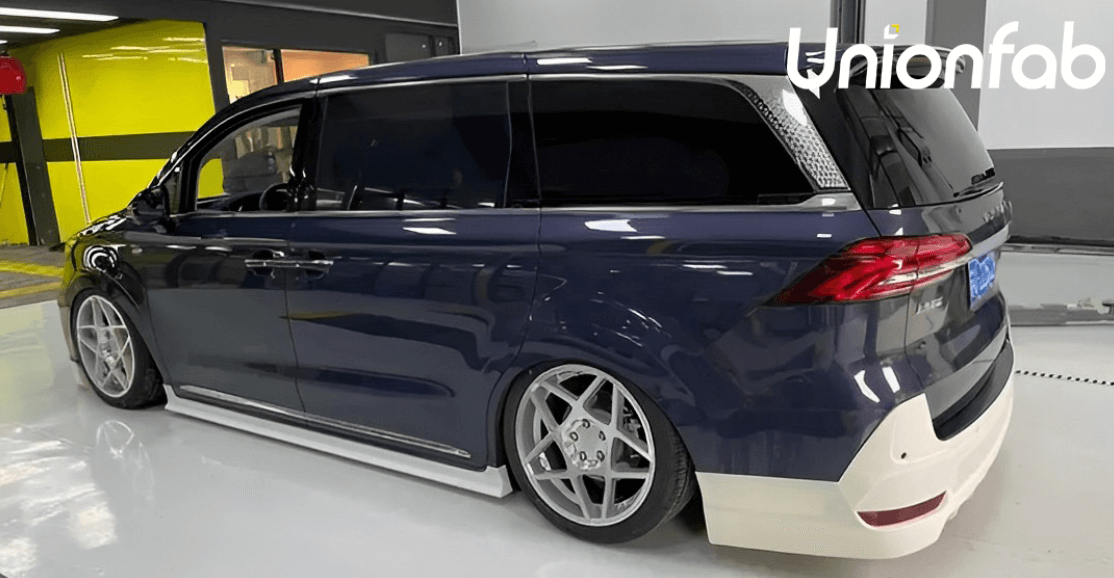
At Unionfab, we don’t just print — we engineer, finish, assemble, and deliver. Whether you're building a custom prototype or scaling production, our large-format systems and experienced team help you go from CAD to real-world part — fast.
Large-Scale Capabilities
Max Build Volume: Up to 2100 × 900 × 700 mm in a single print
Supported Technologies:
3D Printing Technologies: SLA, FDM, SLS, SLM, and more
CNC, casting and molding for hybrid/scalable production
Material Library: Over 80+ options including PLA, PETG, ABS, Nylon, Tough Resins, and CF composites
Beyond the Print: Seamless part segmentation, precision assembly, advanced finishing
Full-Service Manufacturing Support:
✅ Design-for-Additive consultation
✅ Post-processing (sanding, coating, painting, CNC trim)
✅ Structural bonding & assembly
✅ Secure global delivery and customs clearance
Get Your Quote Today
Conclusion: Think Big, Print Bigger
Large-format 3D printing isn’t just a manufacturing upgrade — it’s a mindset shift. Whether you’re prototyping a 2-meter vehicle panel, building a custom industrial fixture, or launching an eye-catching exhibition piece, the right combination of technology, materials, and expertise makes all the difference.
Have an oversized idea in mind? Let Unionfab help you make it real — with professional guidance, world-class SLA capabilities, and reliable global delivery.
Get a free quote today →Let’s bring your biggest ideas to life — one layer at a time!
![[object Object]](https://ufc-dtc-cms.oss-accelerate.aliyuncs.com/blog/20240712/112103_uq04lrzvu.png)