3D Printing vs. Injection Molding: Full Comparison by Cost, Speed & Flexibility
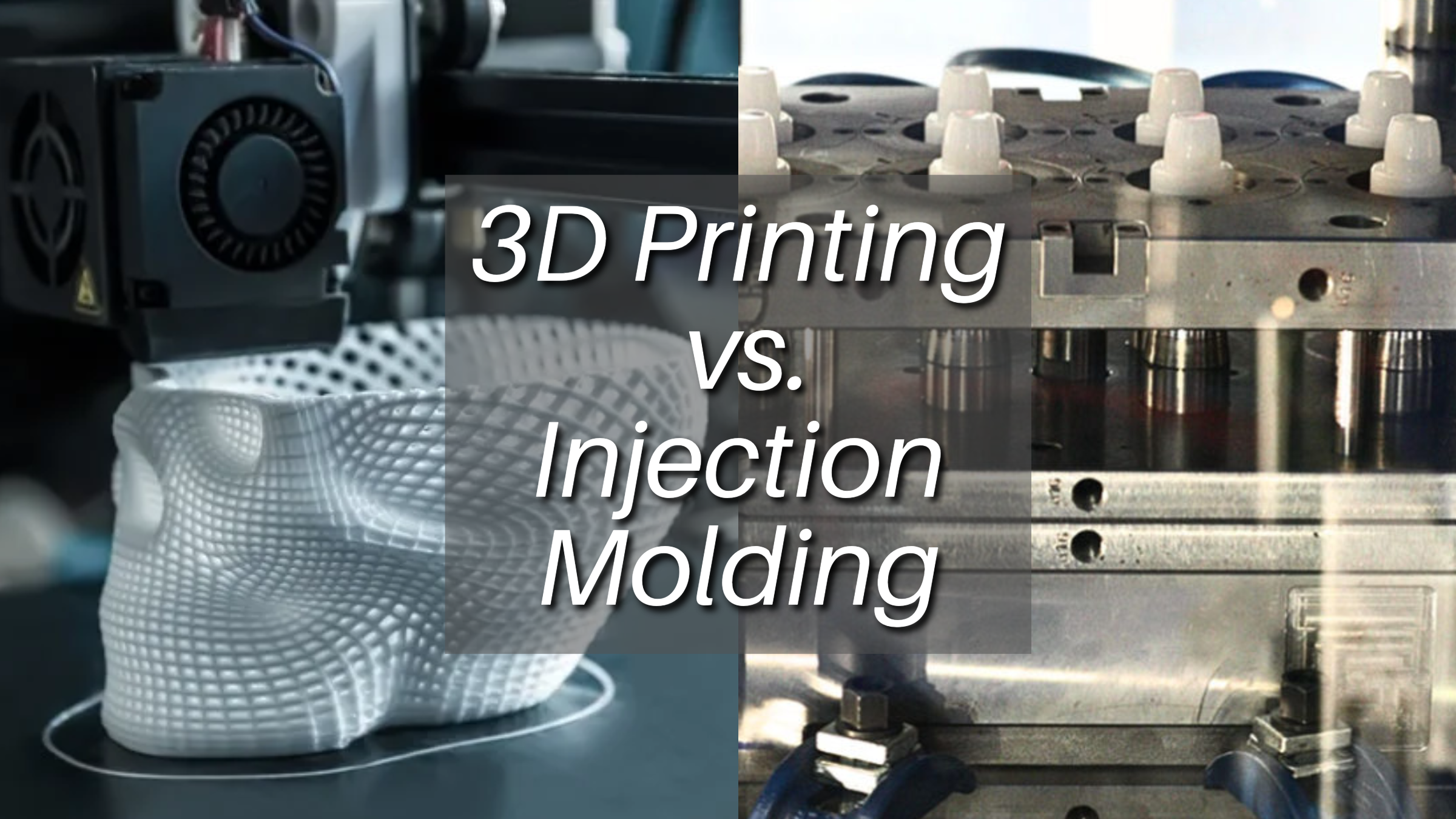
Whether you're launching a hardware startup, customizing a medical device, or scaling a best-selling product, choosing the right manufacturing method is crucial to your success. Do you need flexible design and rapid prototyping? Or is cost-per-unit your biggest concern for scaling?
In this guide, you’ll learn:
How to evaluate 3D printing vs. injection molding by cost, speed, and volume
When to choose each based on your product stage
How hybrid strategies can reduce risk and shorten time-to-market
Let’s explore both technologies side-by-side.
Overview of Both Technologies
What is 3D Printing?
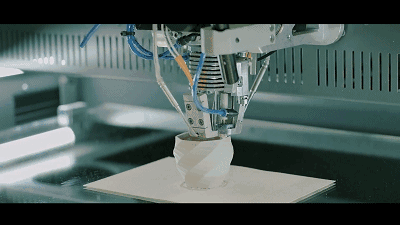
3D printing (additive manufacturing) builds parts layer by layer from a digital model — no tooling, no mold. It supports highly complex geometries that traditional methods can't handle.
Common Methods:
SLA – High-precision resin parts
SLS – Strong nylon parts with no support needed
FDM – Low-cost thermoplastic prototyping
MJF – Fast, accurate multi-part printing
Best for:
Rapid prototyping
Customized or low-volume parts (1–500 units)
Complex design testing
Used in: Healthcare (custom implants), electronics (enclosures), automotive R&D
3D Printing Applications:
Industry | Common Applications | Unionfab Case 1 | Case 2 |
---|---|---|---|
Medical & Dental | Surgical guides, | ![]() | ![]() |
Consumer Products/Electronics | Concept casings, | ![]() | ![]() |
Industrial Design | Functional testing, | ![]() | ![]() |
Automotive | Interior mockups, | ![]() | ![]() |
Need parts in days, not weeks? With 3D printing, you can go from CAD to real-world prototype faster than ever. No tooling. No delays. 👉 [Start Printing Today →]
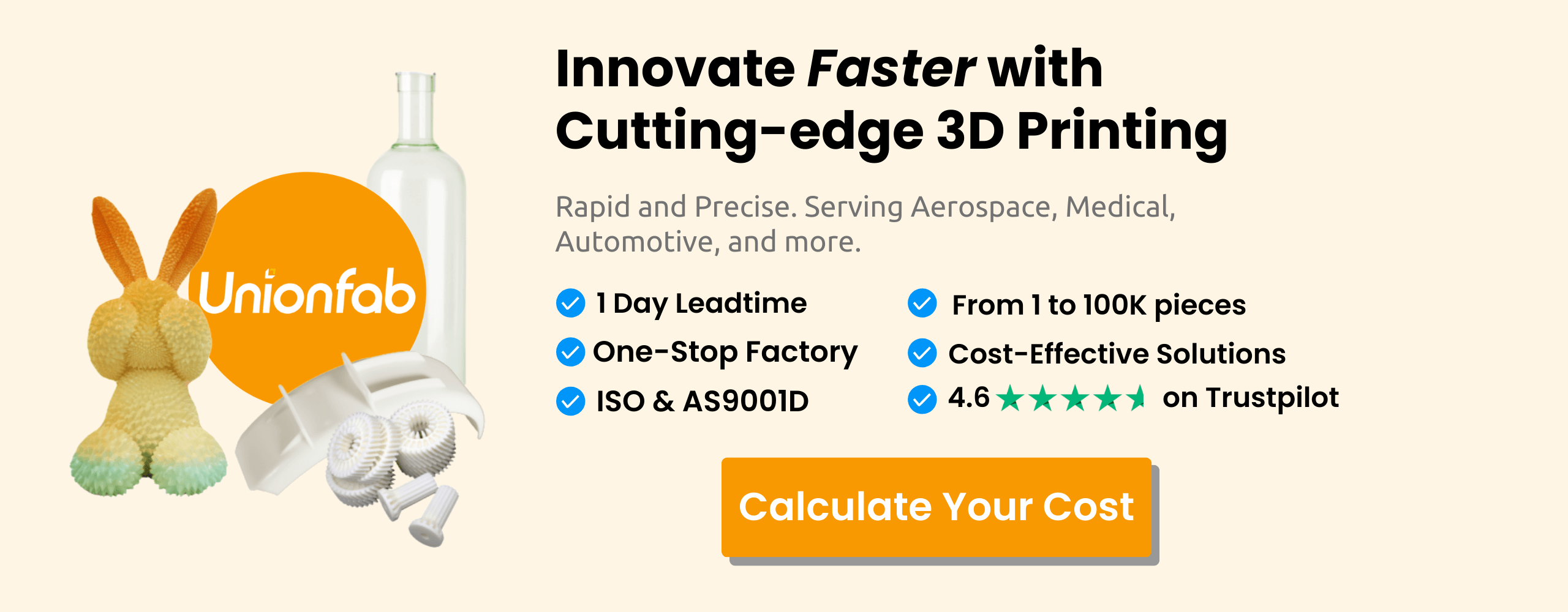
What is Injection Molding?
Injection molding melts and injects plastic into a steel or aluminum mold. Once the mold is made, it produces identical parts at high volume with unbeatable speed and consistency.
Key Highlights:
High upfront tooling cost ($3,000–$15,000+)
Ultra-low per-unit cost at scale (as low as $0.50/part)
Requires mold design considerations (draft angles, parting lines)
Best for:
Mass production (1,000+ parts)
Finished products with precise fit and finish
Long product lifecycles
Used in: Consumer goods, toys, automotive components, packaging
Quick Comparison
Aspect | 3D Printing | Injection Molding |
---|---|---|
Production Method | Additive (layer-by-layer) | Mold-based (material injection) |
Ideal Use | Prototyping / Small batch | High-volume production |
Setup Cost | Low | High (mold fabrication required) |
Ideal Volume | 1–500 parts | 1,000+ parts |
Design Flexibility | Very High (complex geometries) | Moderate (limited by mold design) |
Lead Time | Days to weeks | Weeks to months |
Still not sure which fits your needs? 👉 Talk to our experts today and get a free project evaluation!
In-Depth Comparison: 3D Printing vs. Injection Molding
Cost Comparison
Manufacturing cost is often the deciding factor between 3D printing and injection molding.
Key Differences:
3D Printing | Injection Molding | |
---|---|---|
Mold Needed? | ❌ No | ✅ Yes (custom steel/aluminum) |
Upfront Cost | Low | High ($3,000–$15,000) |
Per-Part Cost | $3–$10 (small batch) | As low as $0.50 (bulk) |
Real-World Cost Example:
Volume | 3D Printing | Injection Molding |
---|---|---|
500 units | ~$4,000 ($8/unit) | ~$7,000 ($6,000 mold + $1,000 parts) |
1,000 units | ~$80,000 | ~$80,000 |
10,000 units | ~$80,000 | ~$11,000 |
Verdict:
For < 500 units, 3D printing is more affordable.
For 1,000+ units, injection molding is cheaper.
For 10,000+ units, injection molding is significantly cheaper. ⠀Use 3D printing when starting small. Switch to molding when scaling up.
Speed & Lead Time
Volume | 3D Printing | Injection Molding |
---|---|---|
500 units | ~$4,000 ($8/unit) | ~$7,000 ($6,000 mold + $1,000 parts) |
1,000 units | ~$80,000 | ~$80,000 |
10,000 units | ~$80,000 | ~$11,000 |
Need a prototype in 2–5 days? Go with 3D printing.
Have stable design and tight deadlines? Injection molding works better at scale.
Volume Suitability
3D Printing | Injection Molding | |
---|---|---|
Best for | 1–500 parts | 1,000–1,000,000+ parts |
Setup Time | None | 3–6 weeks |
Cost Efficiency | High at low volume | Excellent at scale |
Rule of Thumb:
<500 parts → 3D Printing
1,000 parts → Injection Molding
500–1,000? → Consider hybrid (3d prototype → molding)
Design Complexity & Flexibility
3D Printing | Injection Molding | |
---|---|---|
Geometry Freedom | Complex, free-form | Constrained by mold |
Internal Features | ✅ Channels, lattices | ❌ Limited |
Revisions | Easy | Expensive + slow |
Example: A part with internal cooling channels or lattice structures — only feasible with SLS or MJF 3D printing.
Verdict: Go 3D when your design pushes boundaries.
Sustainability & Waste
3D Printing:
Additive = minimal material waste.
Materials often recyclable or reusable (e.g., PA12 powder in SLS).
Injection Molding:
Generates more waste in setup and sprues.
Better for recycled pellets, and many shops support material reclaiming.
3D printing is more efficient for short runs. Molding is more efficient over long-term scale.
Iteration & Prototyping
3D Printing:
Perfect for rapid design testing.
Update CAD → reprint in hours.
No tooling lock-in.
Injection Molding:
Mold design changes are costly and time-consuming.
Each modification may require a new mold or mold rework.
Conclusion: In early-stage development, nothing beats 3D printing’s agility.

When Should You Use 3D Printing or Injection Molding?
When to Choose 3D Printing
3D printing is your best bet when speed, design freedom, or short-run production is mission-critical. It lets you move fast, test ideas, and avoid large upfront costs — especially useful at the prototype or pilot stage. Use 3D printing if:
You’re prototyping a new product and need parts within days
Your design includes complex features (e.g., internal channels, undercuts, lattice)
You need 1–500 units for pilot runs or custom variations
You want to validate your idea before investing in a mold
You’re building functional prototypes or MVPs
💡Tip: 3D printing also allows design revisions without retooling — perfect for iteration cycles.
When to Choose Injection Molding
Injection molding becomes the smarter option once your design is finalized and you're ready to scale. It offers unbeatable unit economics at volume and ensures a consistent, high-quality finish for every part. Use injection molding if:
You’re launching a mass production run (1,000 to 1,000,000+ units)
Unit cost is a key driver of your profit margin
You require specific materials or finishes like high-strength ABS, optical clarity, or textured surface
You’ve locked the design and don’t expect major changes
⠀💡Note: Tooling is a long-term investment. Best used when you’re confident in product-market fit.
Hybrid Strategy: Iterate Fast, Scale Smart
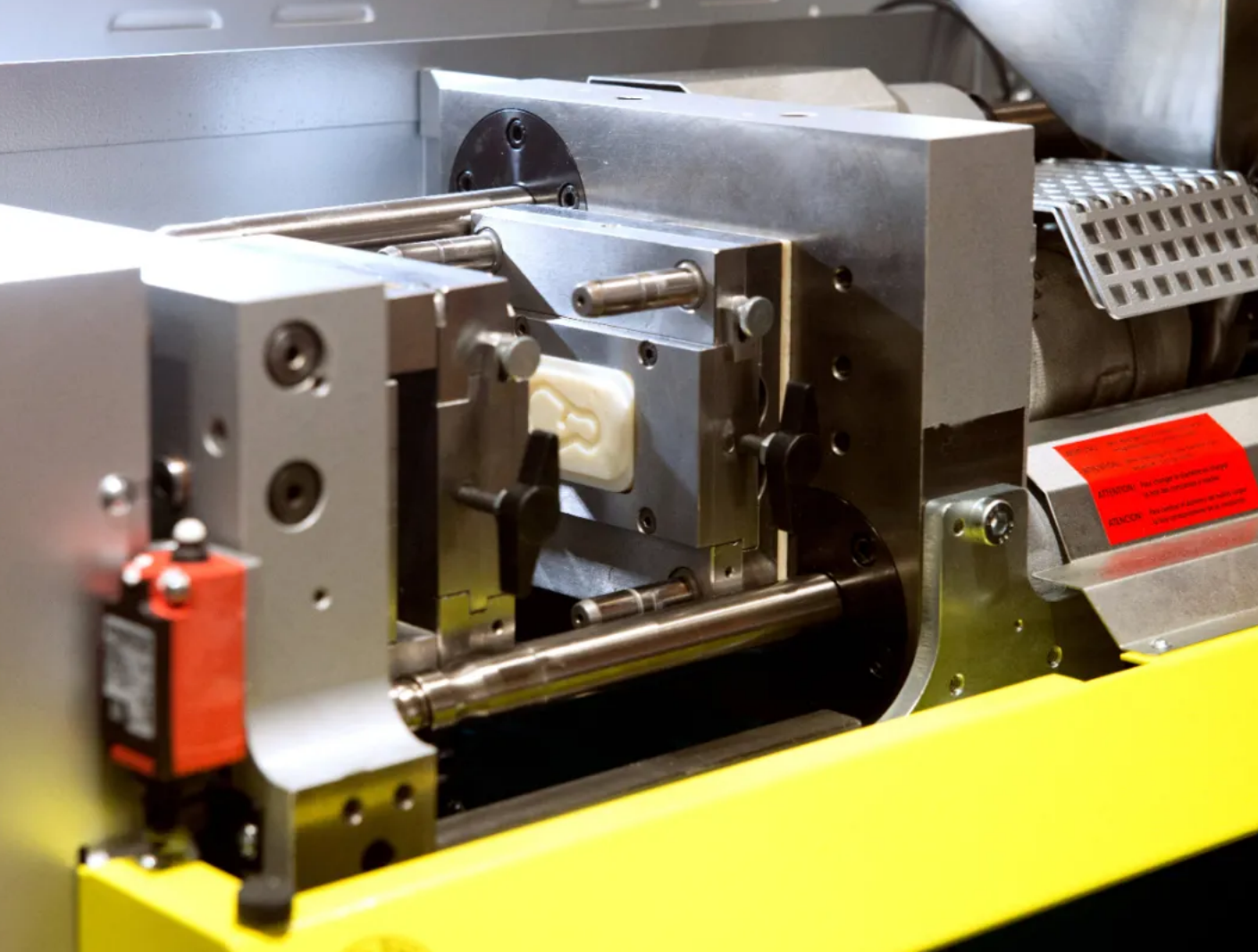
Source: Unionfab
Why choose one when you can combine the strengths of both? The hybrid approach is ideal for teams that want to test and refine quickly, without sacrificing long-term production efficiency.
It allows you to use 3D printing to prototype, validate, and build momentum, then switch to injection molding to scale affordably.
Use a hybrid approach if:
You’re a startup validating product-market fit
You’re launching a limited series or seasonal SKU
You need samples for investors, retailers, or beta users
You’re unsure about initial demand or design lock
Example Workflow:
3D print 50–100 units for user testing
Gather feedback, revise design
Finalize mold & move to 10,000+ units
💡Hybrid = agility early, efficiency later.
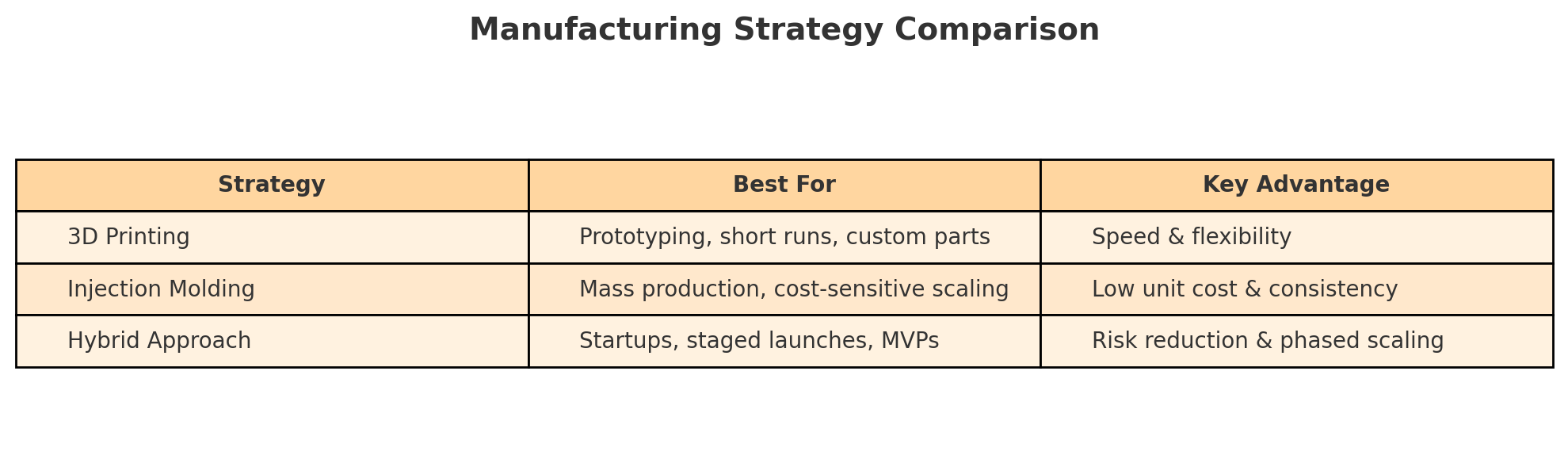