CNC Milling vs. Turning: Processes, Applications, and Pros/Cons
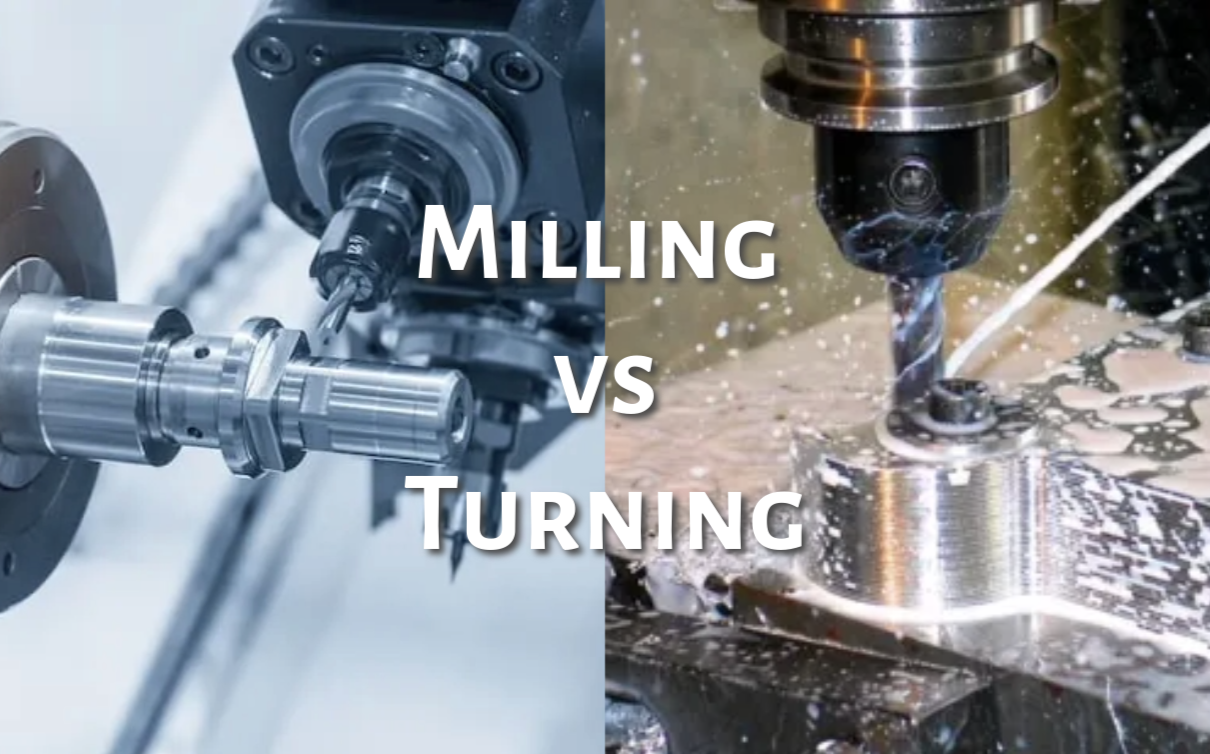
CNC milling and turning are two fundamental types of machining, but they utilize very different processes. This article examines the distinctions between CNC milling and turning, including how each method works, their capabilities and limitations.
CNC Machining: Milling and Turning
Definition and Significance of CNC Machining
CNC machining, short for Computer Numerical Control machining, is a manufacturing process that employs computerized controls to guide the movement of machine tools. This precise control enables the fabrication of complex parts with exceptional accuracy and repeatability.
Traditional manual machining methods have gradually given way to CNC machining due to its ability to reduce human errors, enhance productivity, and produce consistent results across various production runs.
Brief Overview of CNC Milling and Turning
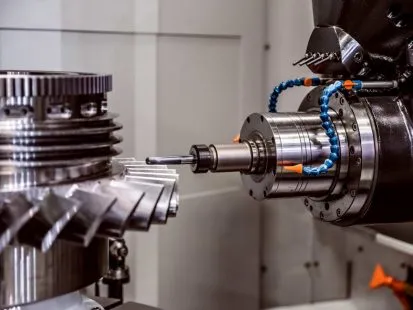
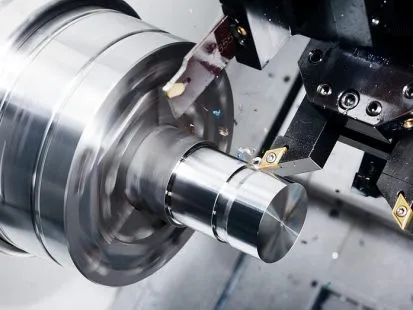
Two of the most common CNC machining processes are milling and turning. Milling utilizes a rotating cutting tool to remove material, while turning rotates the workpiece against a stationary cutting tool.
Both produce precision parts but are suited to different applications. That is why choosing the right CNC machining technique is vital. Factors like complexity of the part, speed, cost, and required tolerances must be weighed when selecting between milling, turning, or other processes.
CNC Milling: Process and Characteristics
Explanation of the CNC Milling Process
CNC milling involves the use of rotary cutters that rapidly remove material from a workpiece to create complex shapes. This process is guided by computer-controlled movements along multiple axes, ensuring unparalleled precision and repeatability.
Overview of CNC Milling Machine Components
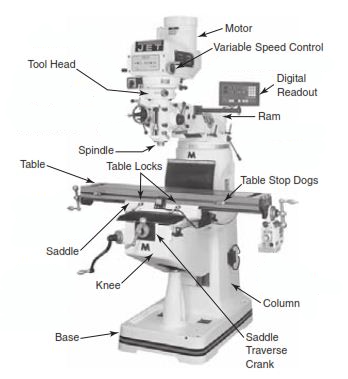
The key components of a CNC mill include:
Spindle: The spindle holds the milling cutter, rotating it to perform the cutting operation.
Worktable: The worktable holds the workpiece and can be moved along multiple axes to position it for milling.
Ram: (for vertical machines) The ram can be moved vertically up and down the column, moving the cutter towards or away from the workpiece to adjust cutting depth.
Arbor: (for horizontal machines) The arbor is a cylindrical tool holder that supports the milling cutter on a horizontal milling machine.
Column: The column supports the spindle and other components, providing stability to the machine.
Knee: The knee is a vertically adjustable platform that supports the worktable and can be adjusted for different vertical positions.
Saddle: The saddle moves along the machine’s horizontal axis and holds the table or other components.
Cutting Tools: Various types of milling cutters, such as end mills and face mills, are used for different milling operations.
Control Panel: The control panel allows operators to input instructions and control various parameters for the milling process.
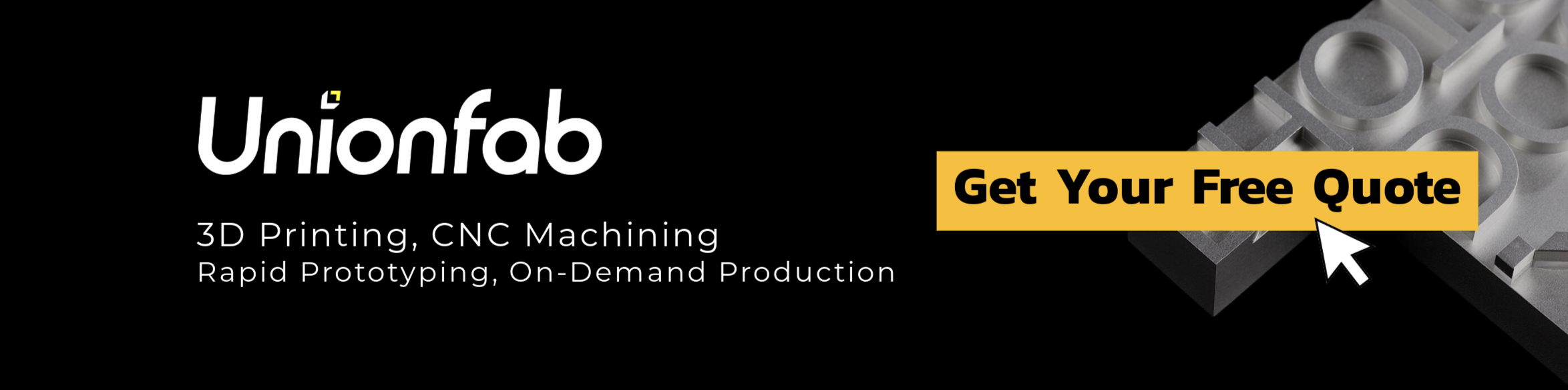
Types of Milling Operations
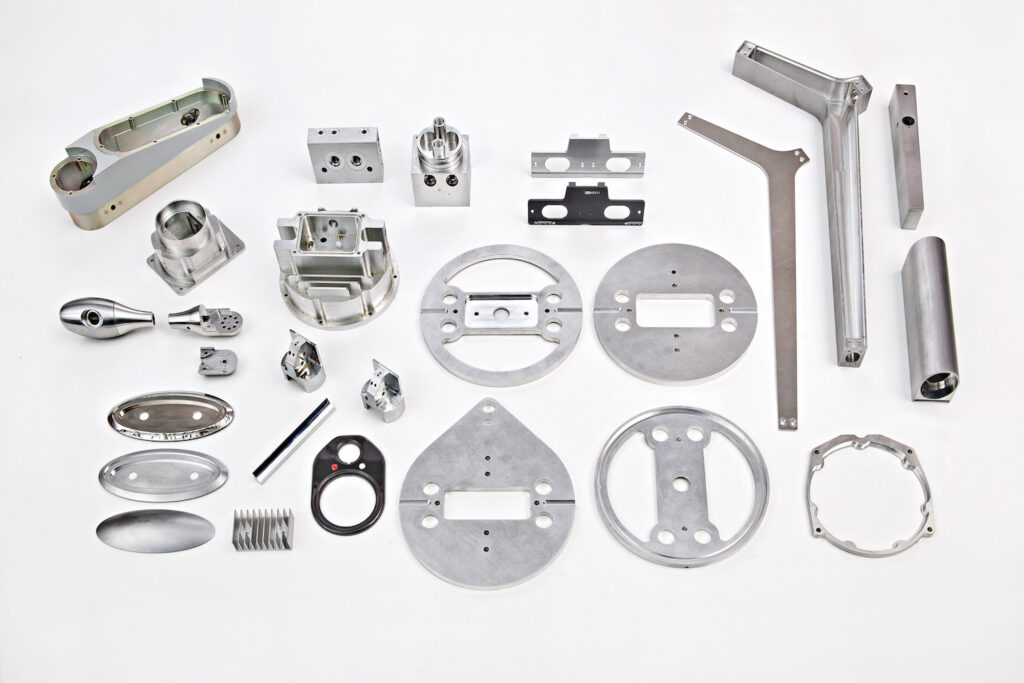
CNC milling encompasses several operations, each tailored for specific outcomes:
Face Milling: Creates flat surfaces by removing material from the workpiece’s face.
Plain Milling: Produces large flat surfaces and can be used for creating slots or pockets that are wider than the cutter's width.
End Milling: Cuts along the sides of the milling cutter, suitable for creating slots, pockets, and intricate profiles.
Profile Milling: Achieves intricate shapes by tracing along the workpiece’s contour.
Drilling and Tapping: Creates holes and threads using specialized cutting tools.
Engraving: Produces detailed designs or text on the material’s surface.
CNC Milling Capabilities and Limitations
CNC milling boasts versatility in generating intricate shapes, detailed designs, and precise features. It excels at crafting slots, pockets, threads, and engravings with consistent accuracy.
However, when dealing with hard materials like stainless steel, milling speeds can be slower due to increased tool wear, frequent tool changes and challenges in achieving desired surface finishes.
Materials Suitable for CNC Milling
CNC milling is highly versatile and can handle a wide range of materials, including metals (aluminum, steel, brass, copper, etc.), plastics (acrylic, PVC, nylon), composites, and even some ceramics.
Milling is particularly well-suited for materials with varying hardness, toughness, and properties. It can efficiently cut through both soft and hard materials.
CNC Turning: Process and Characteristics
Explanation of the CNC Turning Process
In CNC turning, the workpiece rotates against a fixed cutting tool, enabling computer-guided exterior material removal.
The cylindrical symmetry involved suits turning for precision manufacturing of shafts, pins, and other rotationally symmetric parts.
Components of Lathe Machines
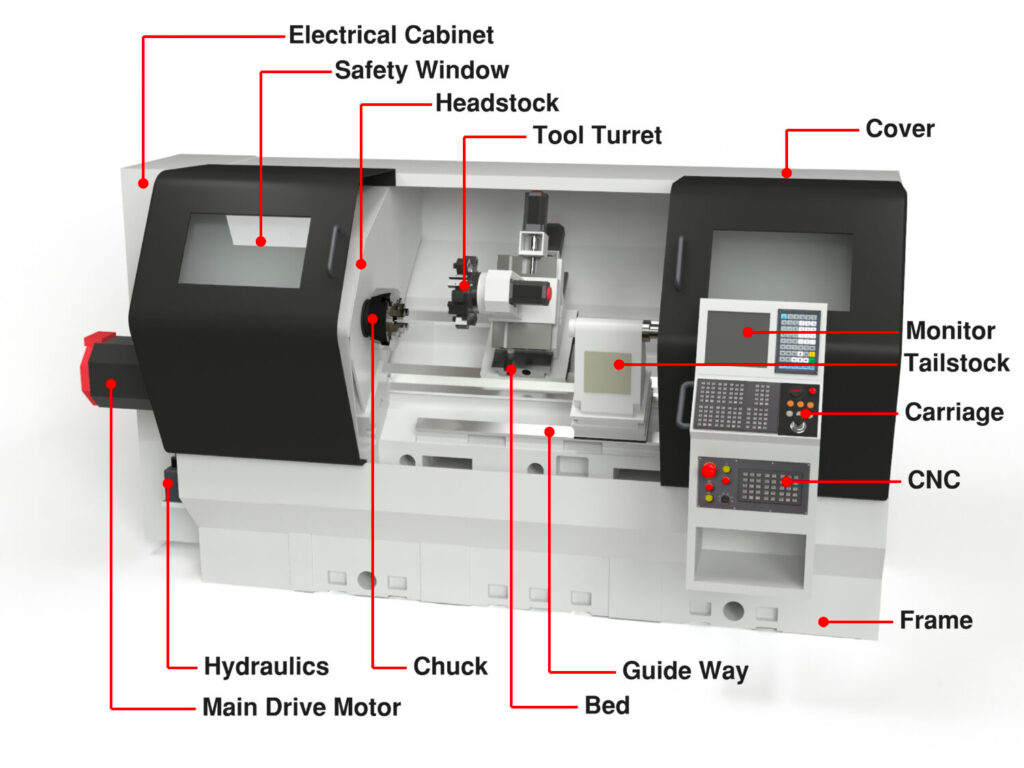
The main machine used in CNC turning is a CNC lathe (also known as CNC turning center). The key components of a CNC lathe include:
Chuck: The chuck holds the workpiece and rotates it during turning operations.
Tool Holder: The tool holder holds cutting tools and positions them to cut the workpiece.
Carriage: The carriage moves along the lathe’s bed and holds the tool holder and cutting tools.
Cross Slide: The cross slide moves perpendicular to the lathe’s axis and controls the depth of cut and tool movement across the workpiece.
Headstock: The headstock houses the spindle and provides rotational movement to the workpiece.
Tailstock: The tailstock provides support to the other end of the workpiece, often used for drilling or additional operations.
Bed: The bed is the horizontal base of the lathe that provides rigidity and supports the other components.
Control Panel: Similar to milling machines, lathe machines have control panels for inputting instructions and controlling machining parameters.
Different Types of Turning Operations
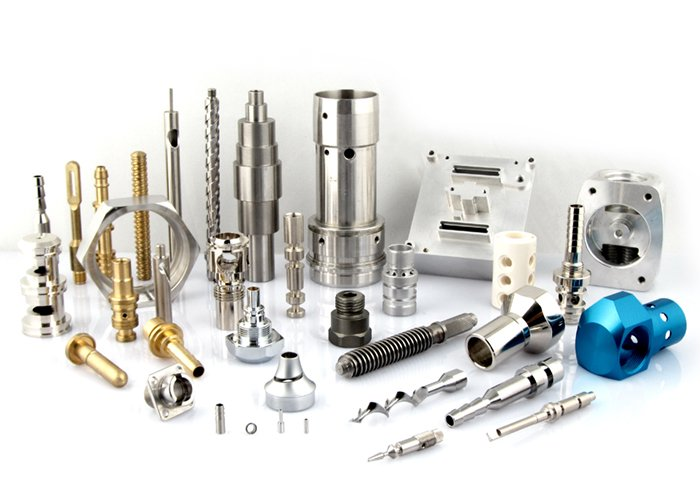
CNC turning encompasses various operations that cater to different machining needs:
Facing: Creates a flat surface on the end of the workpiece.
Threading: Adds precise threads to the workpiece.
Grooving: Produces grooves or recesses in the material.
Boring: Enlarges an existing hole or refines its dimensions.
Knurling: Creates a textured pattern on the workpiece’s surface for improved grip.
CNC Turning Capabilities and Limitations
In CNC turning, the workpiece rotates rapidly as the stationary cutting tool approaches it to remove material. This is advantageous for producing axially symmetric parts requiring high precision and excellent surface finishes.
However, CNC turning has limitations, primarily in terms of complexity. It is best suited for exterior cuts and rotational symmetric parts. Intricate internal features might require additional processes.
Appropriate Materials for CNC Turning
CNC turning is compatible with a wide range of materials, particularly those suitable for rotational symmetry.
Common materials include metals like aluminum, brass, steel, and stainless steel. Materials that are easy to machine, such as certain metals and plastics, are often preferred for turning processes due to their efficient chip removal and minimal tool wear.
CNC milling vs. CNC turning: Key Differences
Direction
Milling: Milling involves stationary cutters with moving workpieces, allowing for versatile shapes.
Turning: Turning rotates the workpiece against a stationary tool, primarily creating cylindrical parts.
Shapes
Milling: Choose milling when your part features intricate shapes, non-rotationally symmetric designs, or requires slots, pockets, and complex contours.
Turning: Opt for turning when your part exhibits rotational symmetry, cylindrical or conical shapes, or requires external cuts with fewer complexities.
Material Choice
Milling: CNC milling can handle a wide array of materials with varying hardness, including metals, plastics, and composites.
Turning is especially suited for rotationally symmetric materials. Wood and composites are generally not well suited for turning given their density and abrasiveness.
Production Volume
Milling: While CNC milling can handle mass production, it is most cost-effective for smaller to medium-sized runs where parts are complex, and precision is paramount. It’s also suitable for prototyping and custom orders.
Turning: Turning excels at mass production due to high speeds and consistency for rotationally symmetric components.
Multi-Axis CNC Milling and Turning
Multi-Axis Milling
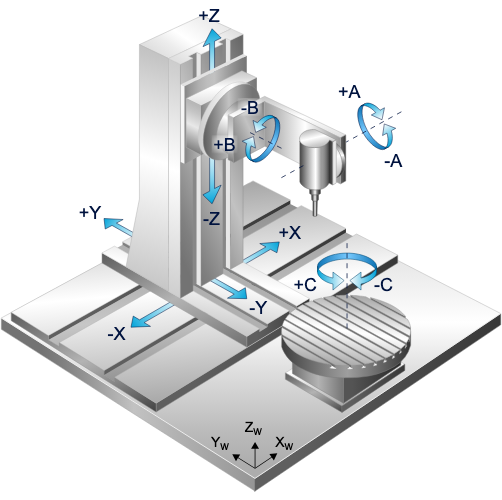
Advanced Movement: Multi-axis milling goes beyond standard 3-axis (X, Y, Z) motion by incorporating additional axes (A, B, C). These added dimensions allow for intricate tilt, rotation, and contouring of the workpiece.
Complex Geometry: This technology enables the creation of complex 3D surfaces, contours, and features from multiple angles.
Examples: Multi-axis milling finds application in tasks like 5-axis turbine blade milling and knee joint machining.
Multi-Axis Turning
Expanded Motion: Multi-axis turning supplements the standard X-Z linear motion with additional linear and rotary axes. This enhancement facilitates the production of components with complex contours, tapers, and grooves at compound angles.
Versatile Operations: It allows for off-center drilling, boring, threading, and milling in a single setup, reducing the need for secondary operations and minimizing work handling.
Examples: Multi-axis turning is employed in machining operations involving components like crankshafts, gears, and propellers.
For further insights into multi-axis CNC machining, please refer to this article.
Applications of CNC Milling and Turning
CNC Milling Applications
Aerospace: CNC milling is vital for crafting complex aircraft components, engine parts, and structural elements that demand high precision.
Automotive: Milling is used to produce engine blocks, transmission components, and intricate automotive parts.
Medical Devices: The medical industry relies on milling for manufacturing implants, prosthetics, and intricate surgical instruments.
Electronics: Milling creates precise circuit boards, housing components, and connectors.
Mold Making: Milling is crucial in mold and die production for plastics and metals, enabling the mass production of consumer goods.
CNC Turning Applications
Automotive: CNC turning excels in producing shafts, bolts, and pulleys used in engines and transmissions.
Medical: Turning is crucial for manufacturing surgical instruments, implant components, and medical devices.
Aerospace: Aircraft components like landing gear pins and hydraulic actuators benefit from turning’s precision.
Oil and Gas: Production of valves, fittings, and drill components.
Consumer Goods: Turning creates parts for everyday items, including knobs, fasteners, and connectors.
Conclusion
Milling provides unmatched versatility for low to medium production of complex, multi-axis parts. Meanwhile, turning enables rapid, high-volume production of rotational components.
Understanding these core differences allows manufacturers to select the optimal process for their specific part requirements in terms of complexity, materials, tolerances, and production volumes.
Partner With Unionfab for Unmatched CNC Services
With expertise in multi-axis milling and turning, companies like Unionfab offer comprehensive CNC machining services tailored to client applications. We produce finished components accurately, efficiently, and economically.
